How 3D-Printed Stainless Steel Succumbs to Marine Corrosion
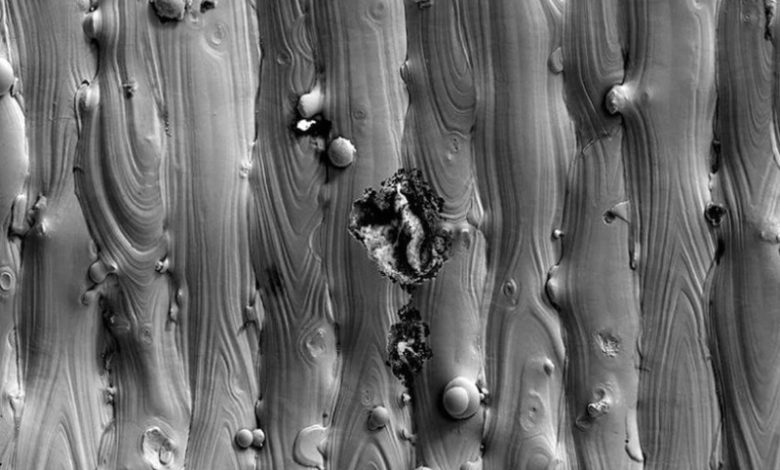
3D-printed stainless steel, once hailed as a revolutionary material, faces a formidable adversary in the marine environment: pitting corrosion. This insidious form of degradation attacks metal surfaces, making it challenging to detect and control.
The Culprits: Slags and Pitting Corrosion
What Is Pitting Corrosion?
In concrete terms, pitting corrosion occurs when a metal undergoes degradation of its protective oxide layer and loses electrons in the process. When present in an aquatic environment, an electrochemical reaction occurs, resulting in the creation of small holes or pits on the metal surface. These tiny pits can weaken the material, leading to structural failures.
The Role of 3D-Printed Stainless Steel
Stainless steel 316L is a popular choice for marine applications due to its excellent combination of mechanical strength and corrosion resistance. However, even this resilient material isn’t immune to the scourge of pitting corrosion. Researchers at the Lawrence Livermore National Laboratory (LLNL) have been diligently studying why 3D-printed 316L stainless steel is prone to pitting corrosion in seawater. Their thorough study aims to uncover the underlying causes of its degradation.
The Mysterious Slags
The key players in this corrosion drama are tiny particles called “slags”. These slags accumulate on the surface of 3D-printed stainless steel during the additive manufacturing (AM) process. But what exactly are these slags, and why do they matter?
- Slags Formation: Slags are produced by deoxidizers such as silicon and manganese. In traditional stainless steel 316L manufacturing, these elements are typically added prior to casting to bind with oxygen and form a solid phase in the molten liquid metal. In conventional manufacturing, slags can be removed using tools like grinders. However, in AM, this type of post-treatment is no longer feasible.
- Stochastic Nature: Pitting corrosion is notoriously difficult to understand due to its stochastic behavior. The severity of the repercussions depends on the depth of the cavities formed by the slags. In seawater, controlling pitting corrosion poses significant challenges, especially for naval vessels.
- Advanced Techniques: To unravel the mystery, the LLNL team employed advanced techniques, including plasma-focused ion beam milling, transmission electron microscopy, and X-ray photoelectron spectroscopy on AM stainless steel components. Through these methods, they closely examined the slags present in 3D-printed metal and drew significant conclusions.
The Quest for Resilient Marine Materials
In the quest for resilient marine materials, understanding and mitigating pitting corrosion in 3D-printed stainless steel is crucial. Researchers continue to explore ways to optimize AM processes, improve material properties, and minimize the impact of slags. As the marine industry shows a growing interest in additive manufacturing, addressing these challenges becomes paramount, particularly concerning metal certification.