Breakthrough in Plastic Recycling: New Process Could Enable Indefinite Reuse of Common Plastics
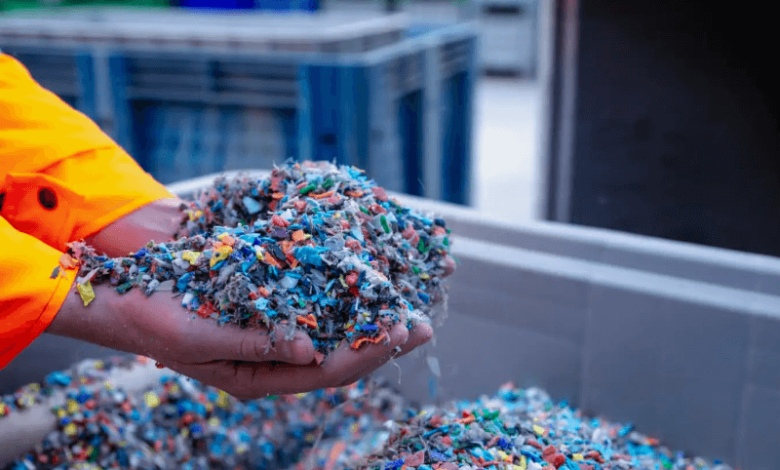
Inventors from the University of California, Berkeley have come up with a new method that could change the face of plastic recycling as is known today. The new method can also decompose most of the well-known types of plastics including polyethylene and polypropylene to their fundamental units that can be reused to produce new plastics without compromising the quality of virgin plastics. Unlike other processes, this process employs cheap and readily available catalysts which could make the process suitable for commercialization. Of course, there are still some barriers, but this invention can be considered as the first attempt to establish a circular economy for plastics and to solve the problem of increasing plastic waste.
To begin with, it is important to realize the fact that the problem of plastic pollution is enormous. Around 5 billion tonnes of plastic waste have been disposed of in the landfills since 1950s. Present day recycling has only been able to recycle roughly 9% of all the plastic that has been manufactured. Recycling methods have been a process that degrades the quality of the plastics each time they are recycled, and are dumped in the landfill after several uses.
A New Way of Recycling Plastic
A team at UC Berkeley headed by John Hartwig has come up with a method of turning waste plastic into vapor and then synthesizing it back into its monomers. This method is effective on polyethylene, the most common plastic in plastic bags and polypropylene used in hard plastic items.
Key features of the new process:
Incorporates easily available and cheaper catalysts such as sodium on aluminium oxide and tungsten oxide on silica.
Is capable of yielding a near 90% efficiency in the process of decomposing the plastic mixture into monomers.
May reduce the presence of such chemicals as dyes and fire retardants during the process
Advantages Over Previous Methods
Prior efforts to perform related processes required costly metal catalysts such as iridium, ruthenium, and palladium but these were lost during the recycling process. Hence, the new method is far more practical for industrial usage due to the availability and low cost of the catalysts required.
Challenges and Future Work
While promising, the technology still faces several hurdles:While promising, the technology still faces several hurdles:
- The results obtained can be further extended with a more diverse set of plastic additives for testing.
- The formation of catalyst structures that are not sensitive to being “poisoned” by some additives
- Managing toxicity and the disposal of the end recycling products
- Hence, scaling up the process for industrial use
- Generalization of the Use of Plastic and Recycling
Scholars warn that this is a great development, but the actual problem of unsustainable production and use of plastics cannot be solved by this technology alone. More effort has to be directed towards the problems of single-use plastics and the general concept of the ‘take-make-dispose’ model.
Still, the creation of this recycling process is a step towards the circular economy for plastics, where materials can be recycled infinitely without degrading the material’s quality.